What is Lean Six Sigma in Alaska?
Contact Us
So many people have heard about Lean 6 Sigma but they don’t know what it is and how it works. In this article, we will help you to get a clear definition of this concept. Lean Six Sigma is basically a process improvement methodology that is designed to remove inefficiency and waste, eliminate problems, and improve working conditions in order to offer a better response to the needs of customers.
It brings together the principles, methods, and tools of Six Sigma and Leans into a single powerful and popular methodology for improving the operations of your organization. The team-oriented approach of Lean Six Sigma dramatically improves business profitability and maximizes efficiency for businesses all over the world. Lean Six Sigma matters a lot as long as you do it right. If you are looking for lean six sigma consulting services, feel free to contact Lean Six Sigma Experts of Alaska.
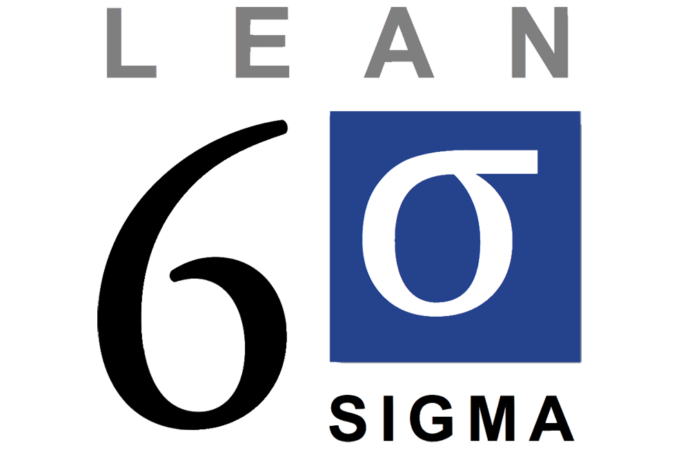
Elements of Lean Six Sigma
There are three main elements of Lean Six Sigma. These include tools and techniques, process and methodology, and mindset and culture. Tools & techniques is a comprehensive set of analytical techniques and tools that are used in identifying and solving problems.
Process & methodology is a series of phases that organize the utilization of problem-solving tools to make sure that you find the true root causes and fully implement a solution. Mindset & culture is a form of thinking which relies on processes and data to attain operational performance objectives and improve continuously.
The above three elements reinforce one another. You cannot use analytical techniques effectively unless you have a process to apply them and a continuous improvement mindset that creates the need for them. Improvement processes won’t produce the desired results in the absence of the techniques and tools which define the process steps activity. There should also be a culture that stresses a systematic data-based approach to problem-solving.
Lastly, you will frustrate the efforts of the culture that seeks continuous improvement if there are no analysis techniques and tools and no methodology or process that you can apply to focus and organize the efforts of improvement. The good thing about the approach of Lean Six Sigma to business improvement is that it includes all these three layers.
What Is Continuous Improvement
Continuous improvement is a business discipline and strategy that was developed from the “Principles of Scientific Management” by Fredrick Winslow Taylor. According to Fredrick Taylor, business is a series of interlocking processes and workflows that you need to use data to manage.
Walter Shewhart created a set of management disciplines for continuous improvement and process management in the 1930s. The disciplines relied on data and were based on the principles of business workflows as put forward by Fredrick Taylor. The Work of Shewhart is the foundation of the management and engineering disciplines of quality control and quality assurance that is available in most modern organizations.
What is Lean?
Toyota developed the concept of Lean as part of its production system. It was designed around the works of Deming and Shewhart. Toyota has been a customer of Deming and used the principles that he taught to establish its operational management practices. Waste elimination is the fundamental driver of Lean. As a result, most scholars define Lean as a set of tools that help in identifying and steadily eliminating waste.
For companies that do high-quantity and large-scale production like Toyota, processes that have wastes in it imply that the company creates high-quantity and large-scale wastes. No single company will want to go through such things. The Lean approach utilizes relevant tools to analyze the various business processes. There are fine main principles of lean manufacturing and these include;
Value: Value is established by what consumers consider to be vital within a service or product. It is not what the individuals who are delivering or developing the service or product consider to be important. Value Stream: This is the set of business steps and activities that are involved in delivering and creating services and products to the customer. It involves connecting the various steps together and not considering every step in isolation. Flow: Refers to the degree at which there exists a smooth and uninterrupted flow of activities which add value to the client. It is the opposite of inefficiency and waste that hinders the flow via the value stream. Pull: The degree at which the value stream only processes products and services of which there exists customer demand. You don’t need to create something and hope that someone will want it. Perfection: Continuously assessing the performance of the value stream to identify that value that is created and improve on it and deliver to the customer instead of restricting changes that enhance the process of delivering and creating customer value. Value
Value Stream
Flow
Pull
Perfection
There are three types of wastes which include Muda, Mura, and Muri. Muda is pure waste or non-value-added waste. Mura is the unevenness in flow and Muri is the burdening of resources beyond the normally rated capability. You can apply the principles of Lean to any business operation or process and not just manufacturing. You can literally apply it to all industries and business functions.
What is Six Sigma?
Motorola was the first company to develop Six Sigma in the late 1980s. Bill Smith, a Quality Engineer, pioneered this methodology to improve how measurement and quality systems work in order to eliminate errors. The systems of Motorola tolerated rates of errors that created a lot of rework, scrap, customer dissatisfaction, and redundant testing.
The focus of the Six Sigma approach was to identify and eliminate all the things that led to variations in the processes. After eliminating the variation, the organization can predict the process results precisely all the time. When the predictable designs are within the range of acceptable performance from the perspective of the customer, it eliminates process errors. Most process changes are ineffective because they don’t get to the root causes of the problems. Over time, organizations would revert to doing things the original way and hence the changes would not stick. Six Sigma is organized into five stages to address these issues.
These include define, measure, analyze, improve, and control. It is crucial to understand what is involved at each stage. The Six Sigma process works with all processes, products, and services that have measurable characteristics and a defined performance objective. The reason is that this methodology relies on data heavily. Combining these two concepts of Lean and Six Sigma is what forms Lean 6 Sigma. Lean Six Sigma Experts of Alaska offers the best Lean Six Sigma certification solutions in the State of Alaska.
There are so many areas or regions where we offer these services with most of them being cities.
However, if you need any of these services, you need to contact us. The list below comprises the areas where we offer these services.